The results are in! (Well, at least the preliminary results).
I spoke to the people at Talas who told me they had no product for my intended use (filling in a loss on a book spine, under deteriorated leather that I can’t lift).
The day I posted last, I took a book from my Library of broken books and fixed it up, attaching mull and false raised bands onto the spine with wheat starch paste (WSP), attached the original boards, inserted new endpapers, and covered the spine with some book cloth. I thought about using leather similar to the one on my client’s book, but I don’t have any old deteriorated leather that turns black and brittle with moisture just sitting around to cover spines with. I chose book cloth because this at least gives a visual indication of moisture.
With that in mind (last week), I bought glass micro-balloons, Beva Gesso-P fine texture, and Flügger Acrylspartel (acrylic putty).
Yesterday I mixed the glass balloons with wheat starch paste, and used a hypodermic needle to inject it into the loss I fabricated.
The WSP displayed the highest moisture content, and was the runniest substance. After 24 hours, it had set, with noticeable shrinkage and significant slump. It was easy to inject with a hypo, and the softest substance I worked with.
The next test was the Gesso. I chose this product primarily because of its description, low moisture, and known (conservation) stability with wood and wood products. The mineral powder suspended in the paste predictably didn’t like being worked through a hypodermic needle- I was forced to remove the needle and enlarge the injection site by cutting a small slit into the book cloth, and injecting it there. The delivery worked okay, but the results were very messy, and is proving very challenging to get out of uncoated book cloth.
It has been in place for 24 hours, and is still soft and malleable under the book cloth, and though it is still setting up, there is some minor shrinkage so far. Upon injection, the book cloth turned dark, and this hadn’t faded over the intervening time. Inspection of the inside of the book revealed that it smelled strongly of Gesso, but nothing had leaked within.
The last product I tested was Flügger. Though I had to fill the hypo without the needle, injection was done with the needle quite easily and with little mess. Flügger displayed the least amount of moisture, fastest setting, with zero slump and unnoticeable shrinkage.
I think, once it’s dry I will cut the spine off and take a look at how the fillers interacted/soaked into/settled in place, and make my final decision on what I’ll use. As of now I’m leaning towards Flügger. I’ve found this report mentioning that Polycell Fine Surface Polyfilla was a superior product, so I’ve ordered some of that online (not easy to find here in the states, surprisingly). When it arrives, I’ll see about putting it in the last loss in my testing spine, and we can compare.
Updates will follow!
Featuring Carson Sams from Carson’s Customs LLC
If you work with your hands or rely heavily on a few specific tools for your job, you’ll know where I’m coming from when I say that bad tools make work so much harder.
When I first got into book restoration, I had bought a minimalist English style skiving (1) knife. Skiving is a very important part of leather preparation- it is thinning down the leather for certain areas of the book where you need to fold it over, or make a smooth transition between the leather and paper or fabric.
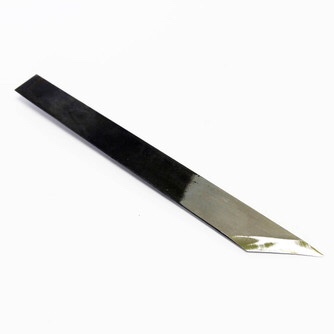
Right-handed English skiving knife
Leather skiving can be tricky though- a dull knife can tear your leather- especially if you have softer goat or sheep leather. You need a very sharp instrument for very careful, detailed work. Needless to say, my first knife was adequate, but not ideal. I found myself having to sharpen it regularly, and stopping work every 5 minutes to strop (2) the edge. In other words, it was cheap, soft metal that wasn’t holding an edge for very long.
Now, my work with the Virginia Renaissance Faire has over the last 12 years put me in touch with some really incredible people with interesting jobs and talents. When I decided I was not going to tolerate my English skiving knife’s issues anymore, I contacted my friend Carson Sams.
Carson (in my estimation) can make anything. My husband and I own several of his pieces- axes, knives, chisels, and other tools. I let Carson know what I was looking for, and we arranged a visit to his blacksmith shop to work on it.
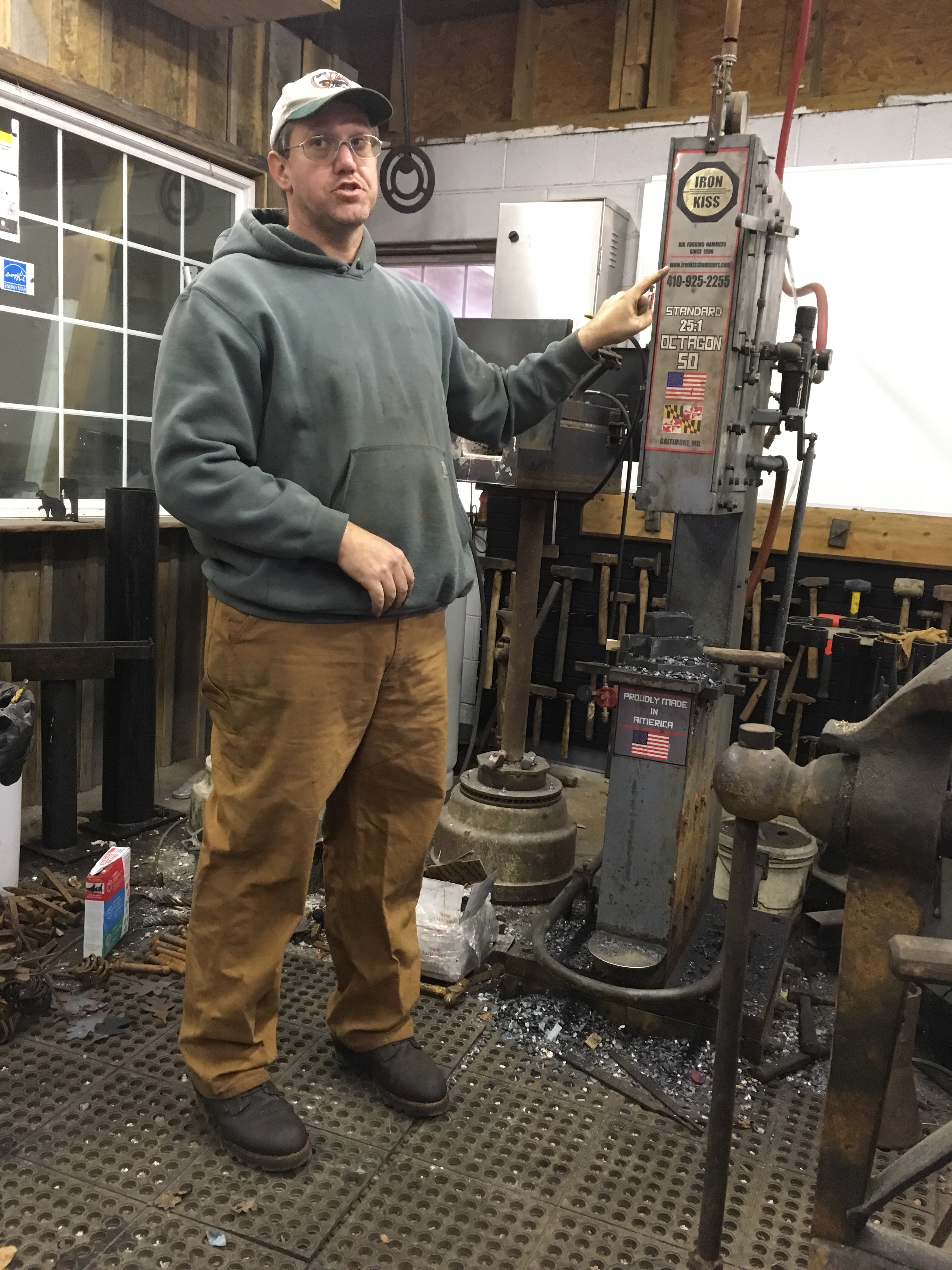
Modifying leather is a craft dating back to prehistoric times, and people in just about every location of the world have developed their own tools for the purpose. There are loads of designs out there to choose from, so I worked with Carson to have a design that was custom for me- one pointed edge, one curved edge, a large hollow ground bevel (concave), and a short and straight bevel for the cutting edge. This was more of a French skiving knife design, differing greatly from the English style.
Carson is known for making knives out of unlikely sources- railroad spikes and chainsaw chains are frequent sources of metal for him. For my request though, he chose his metal carefully- a good thick piece of tool-quality steel.
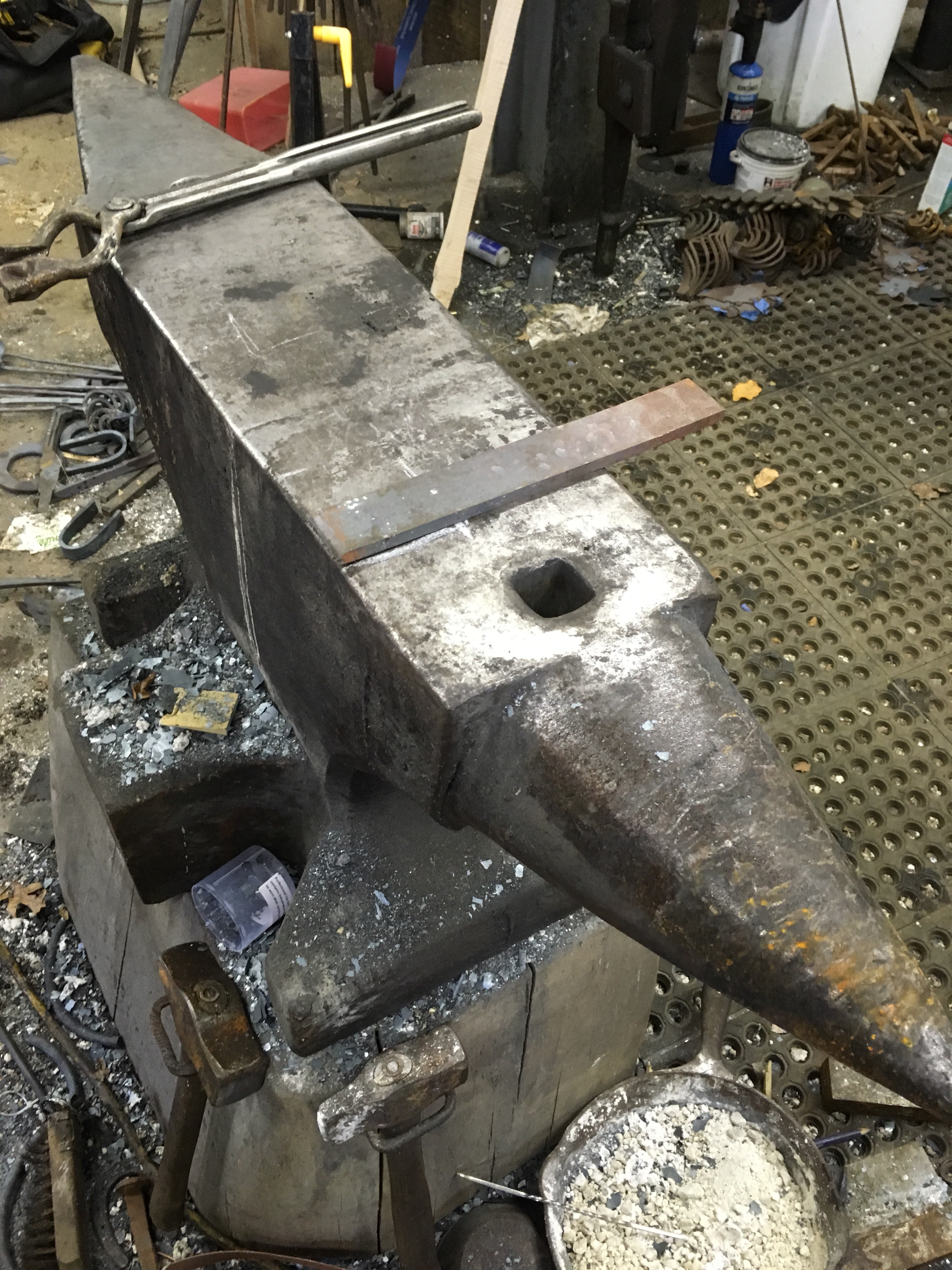
We worked on the dimensions, and he used his power hammer to get the tool stock into shape.
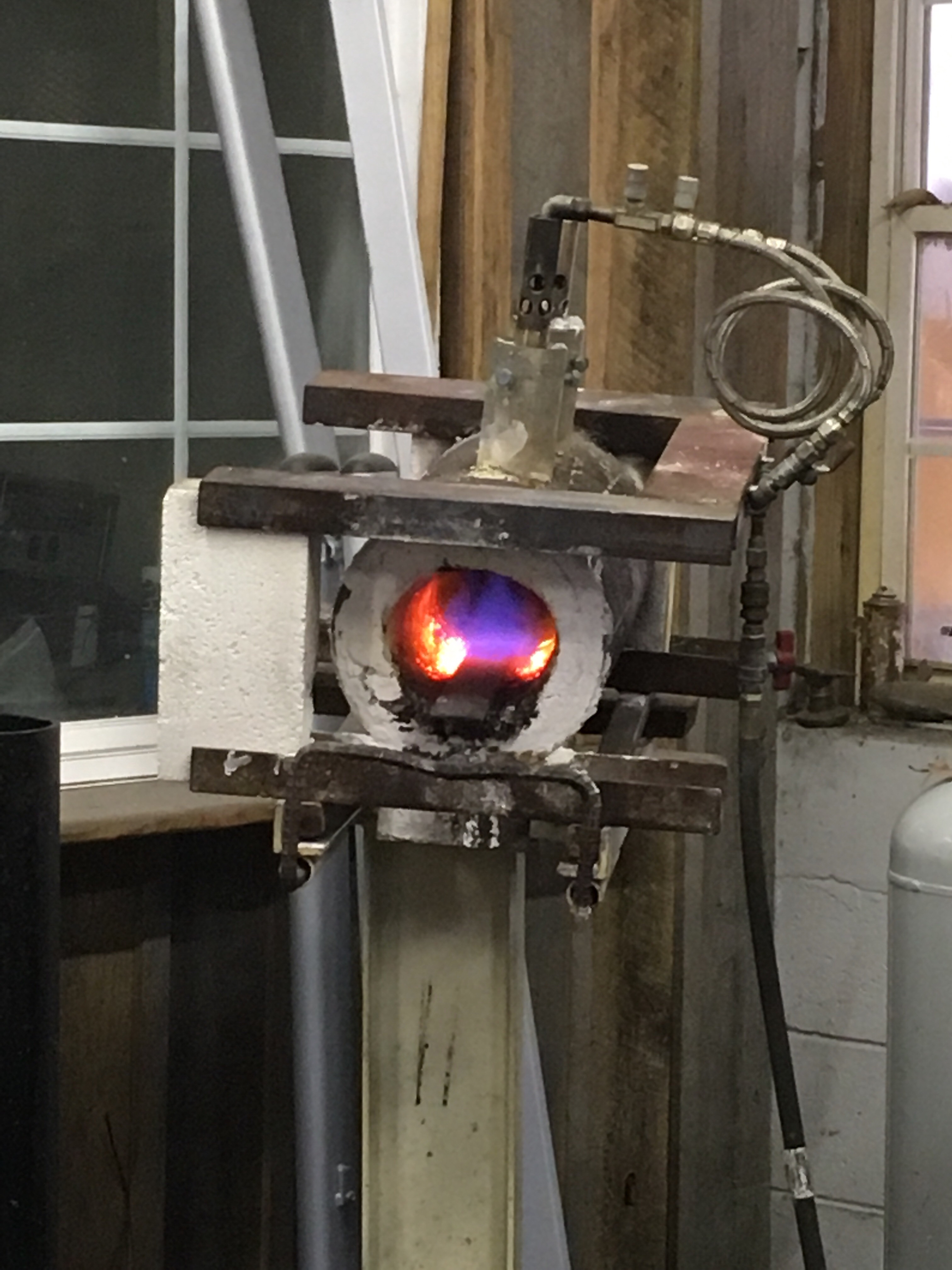
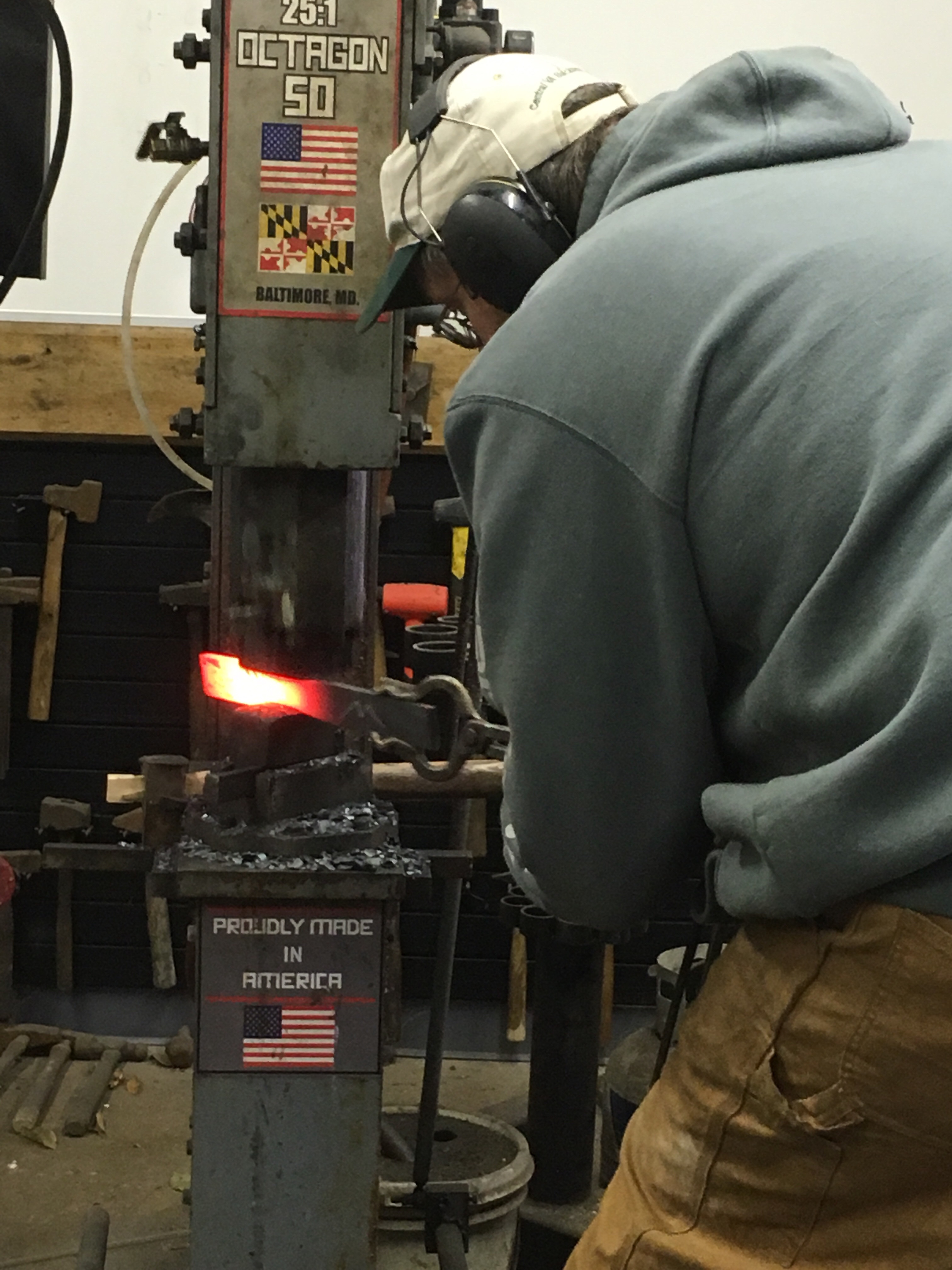
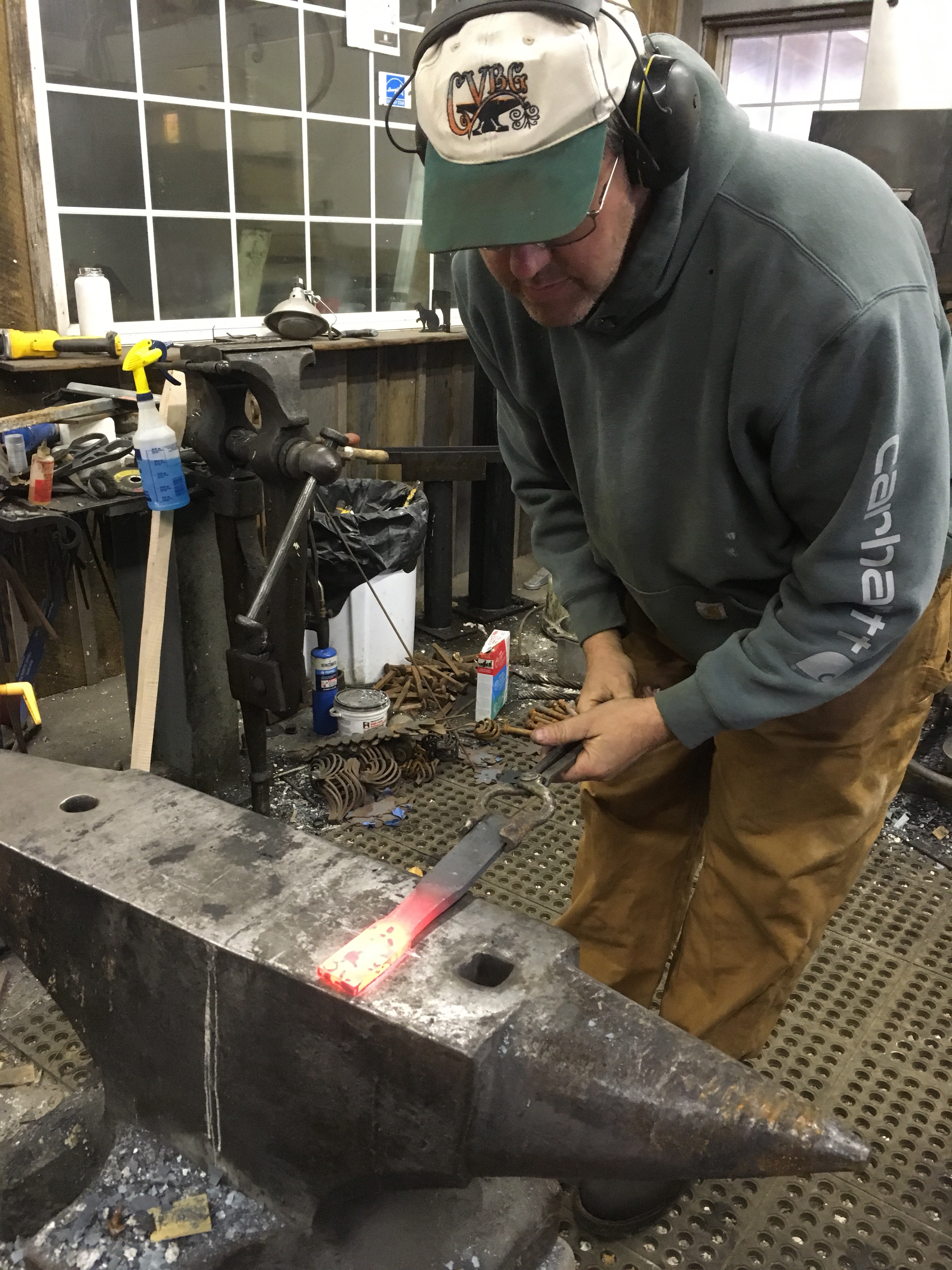
Once the basic shape was achieved, we moved on to the grinder- where apparently, the majority of a blacksmith’s work takes place. Grinding a tool down into its final shape, cleaning up edges, flattening surfaces, polishing and sharpening is no joke- we spent most of the day doing that.
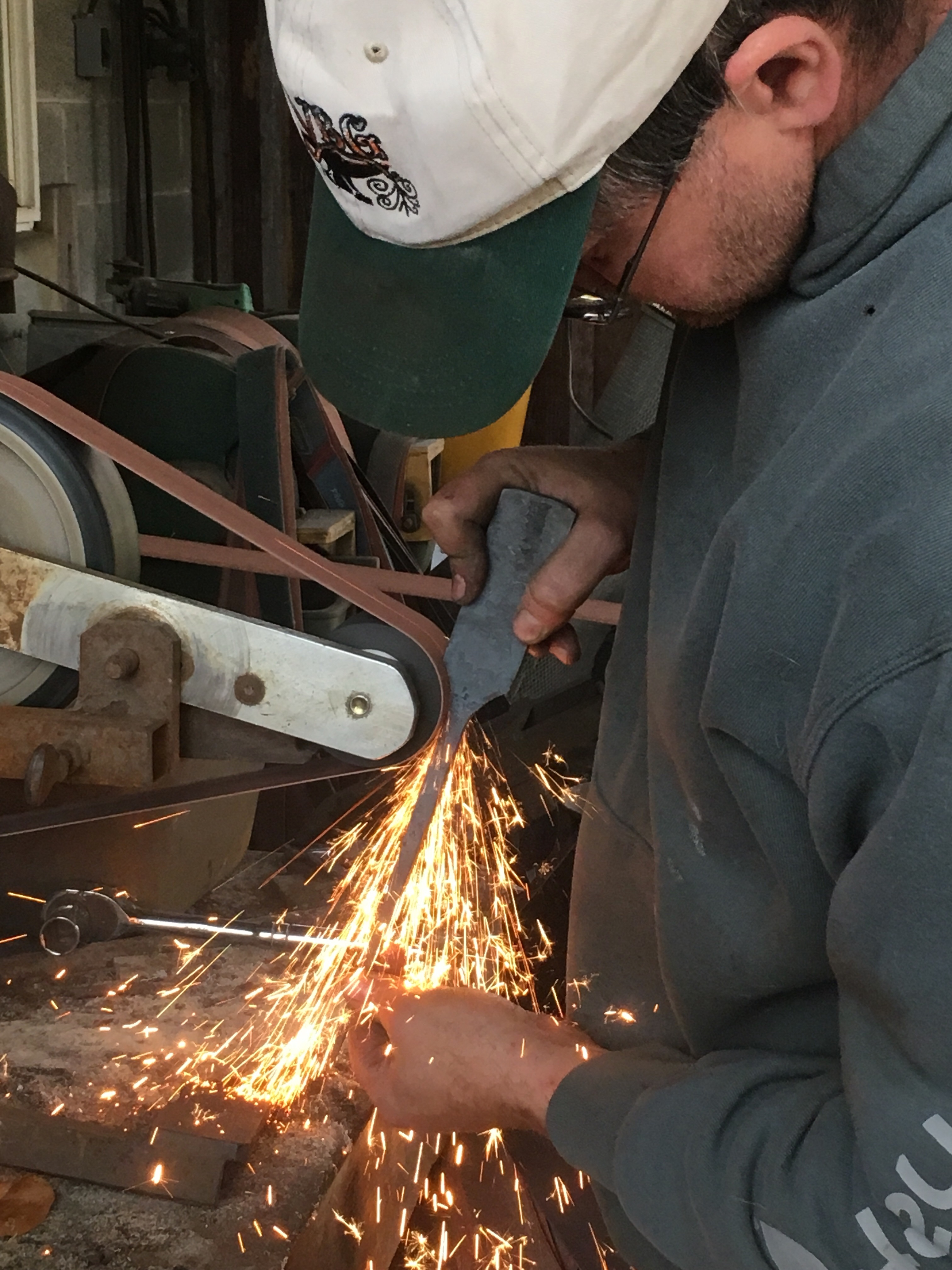
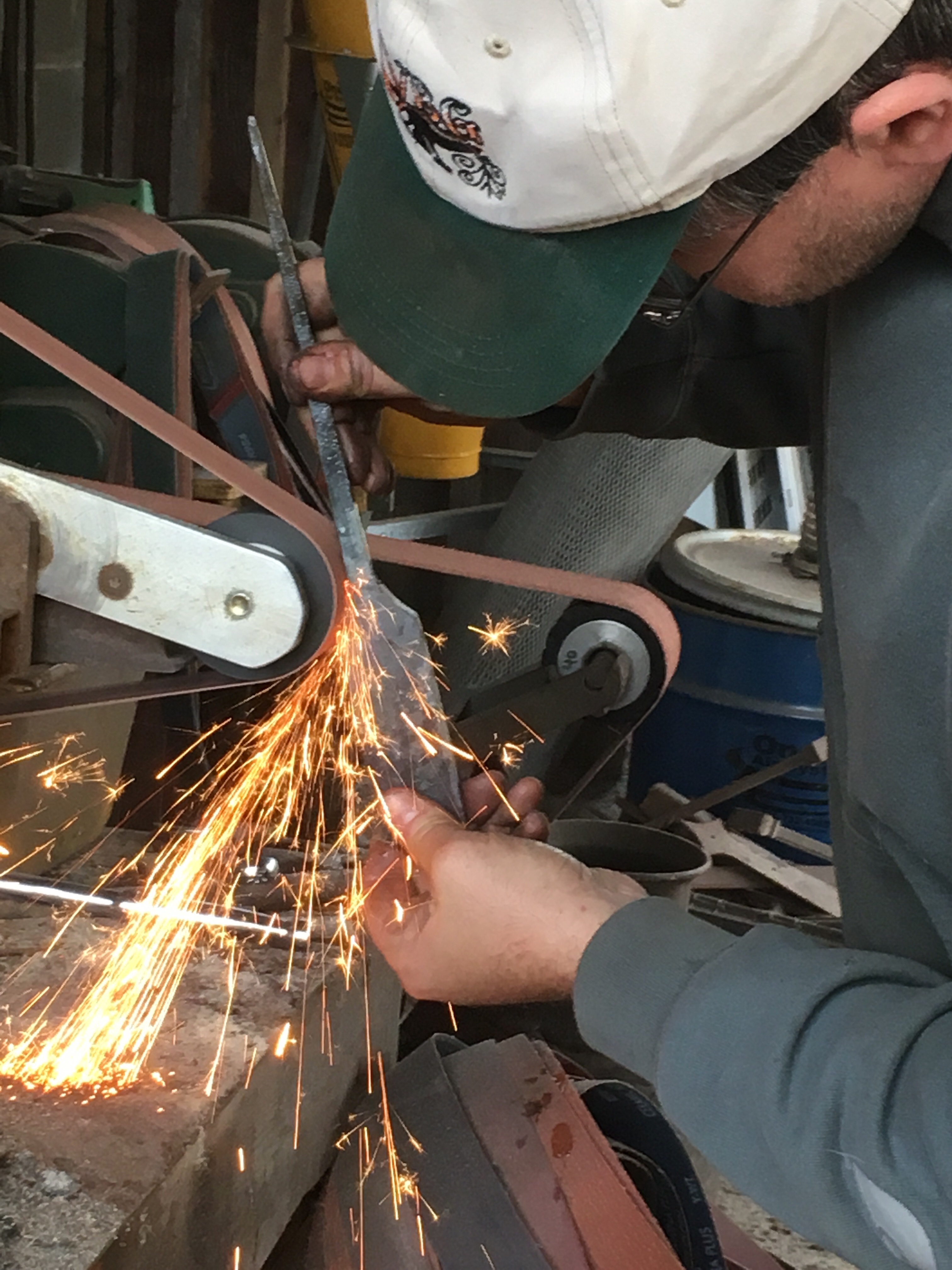
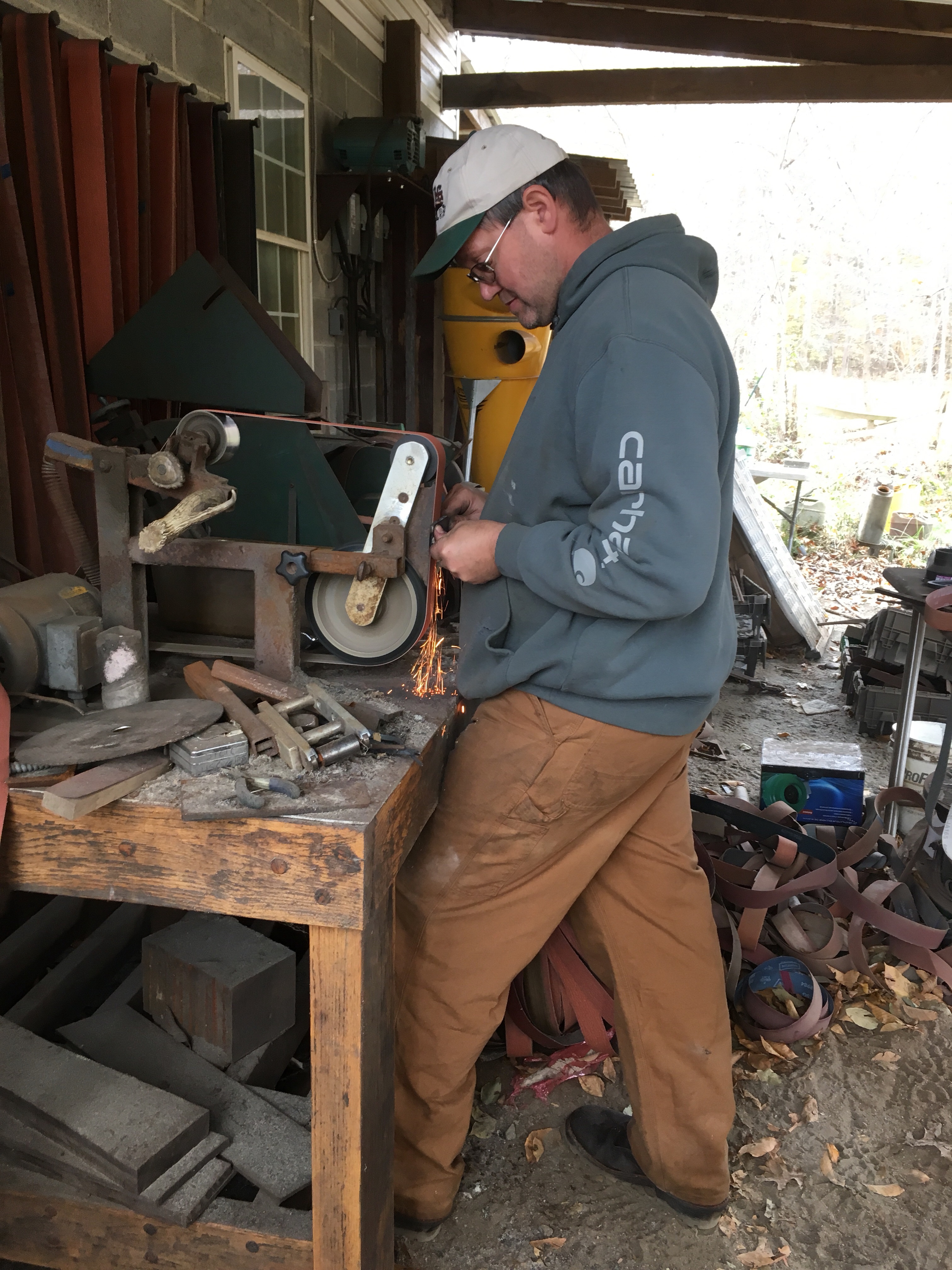
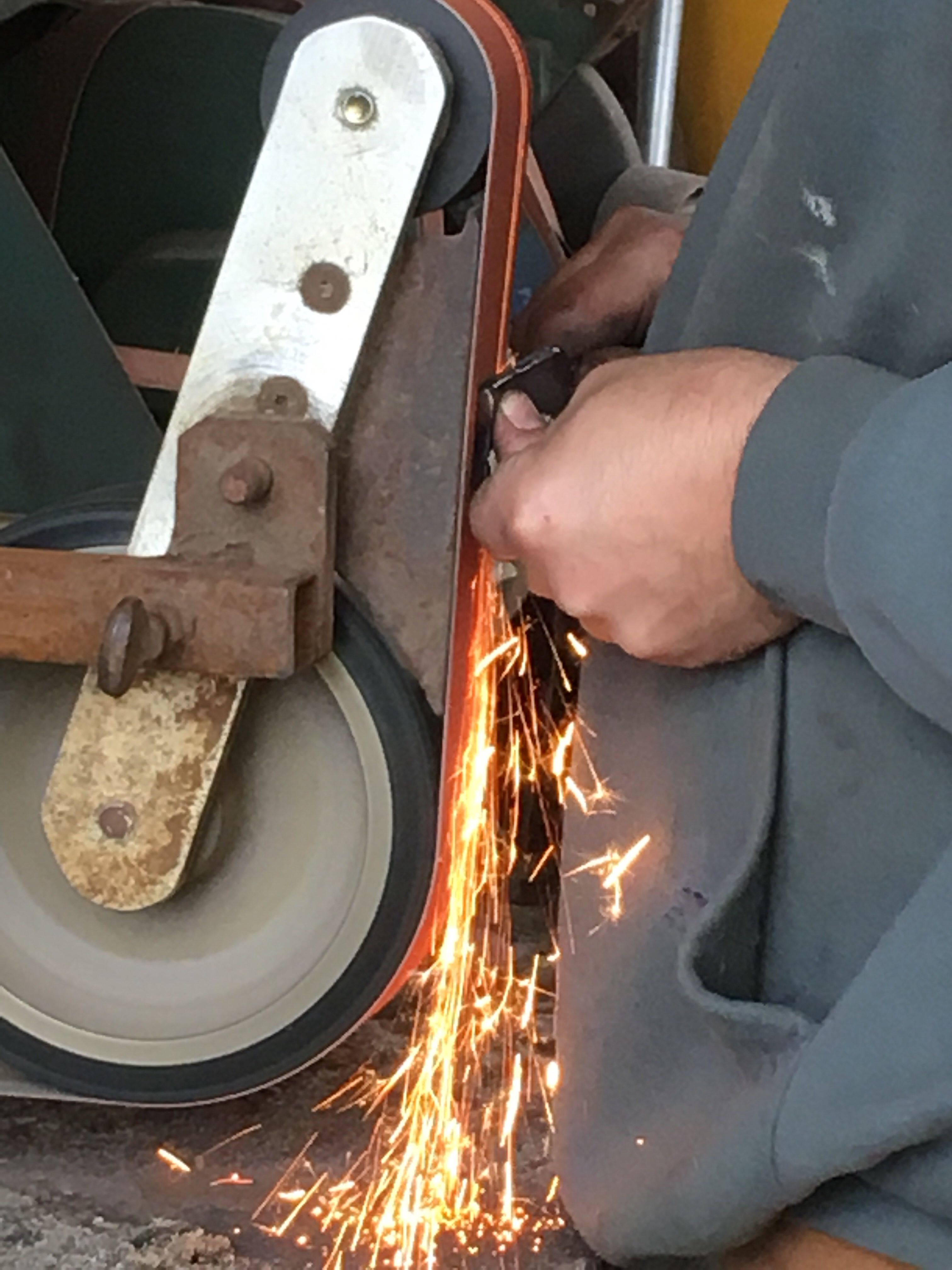
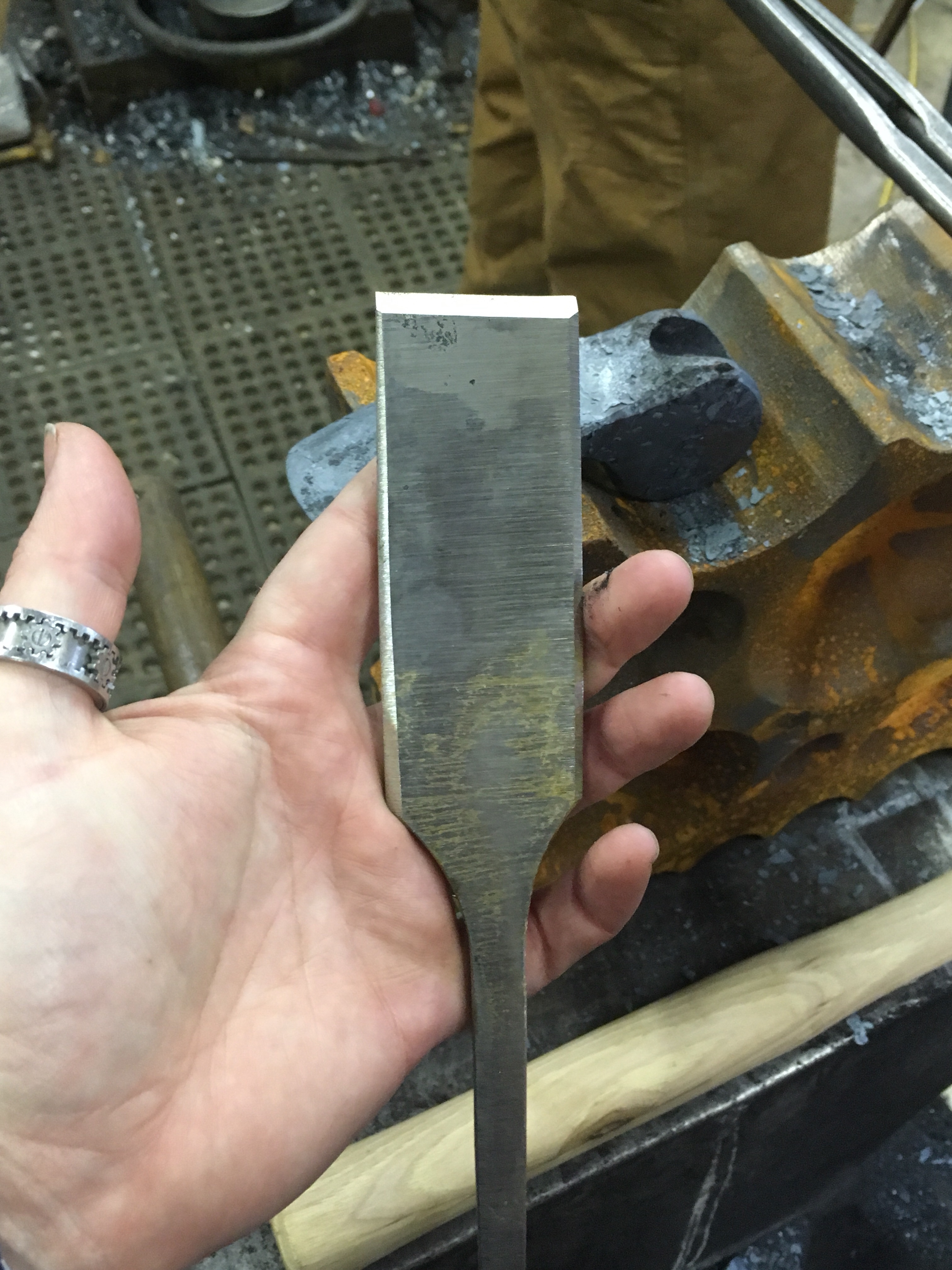
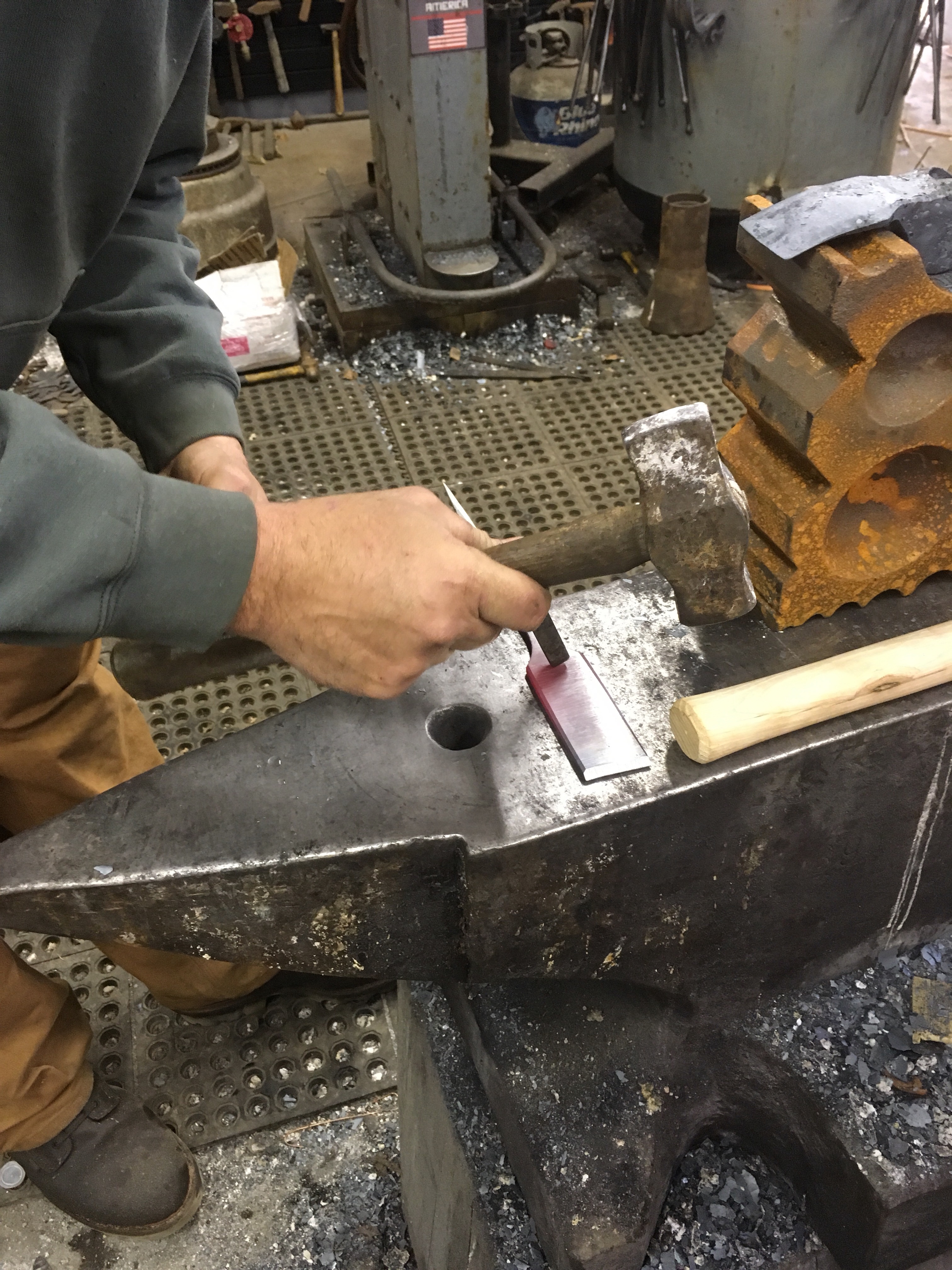
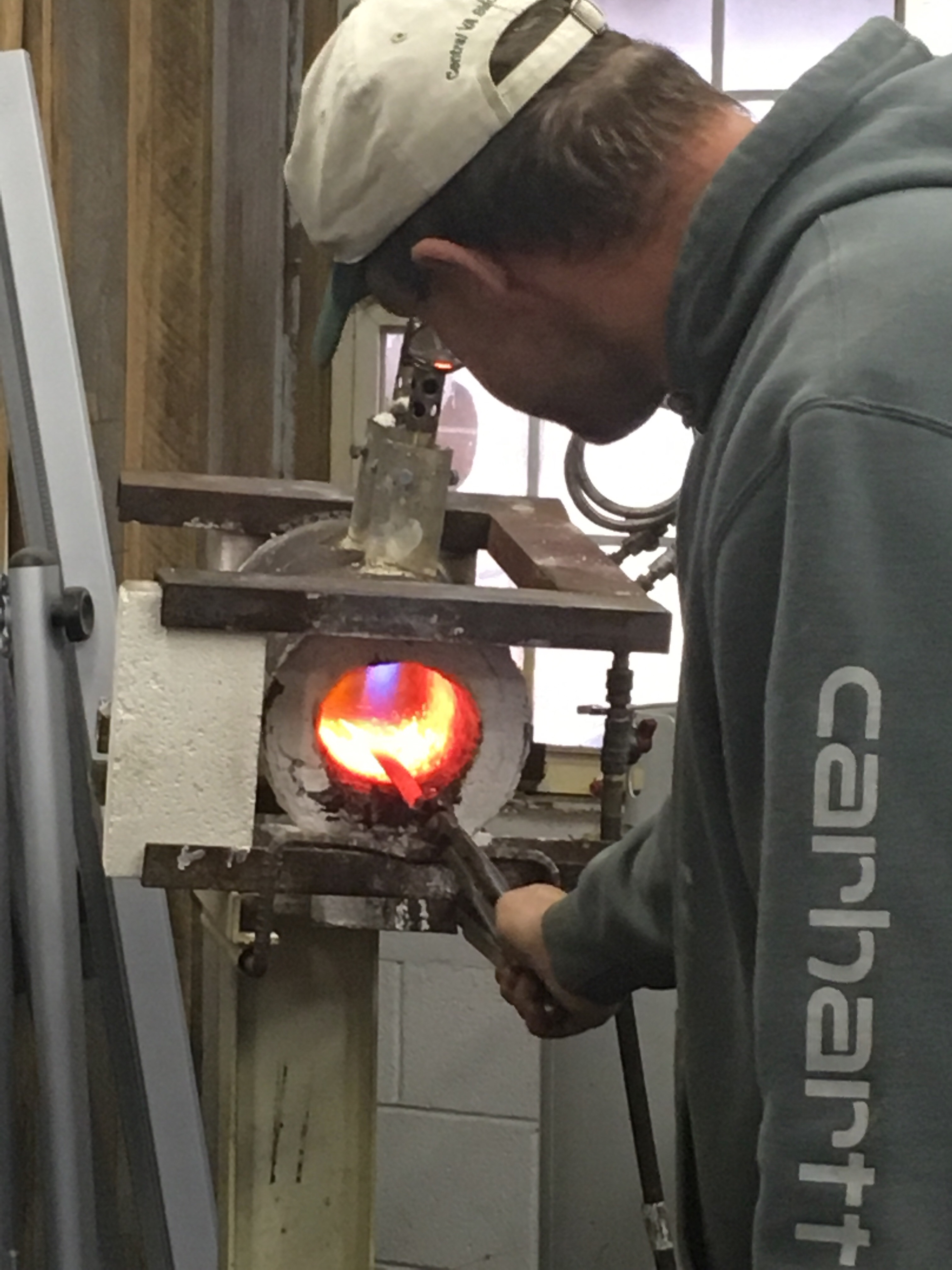
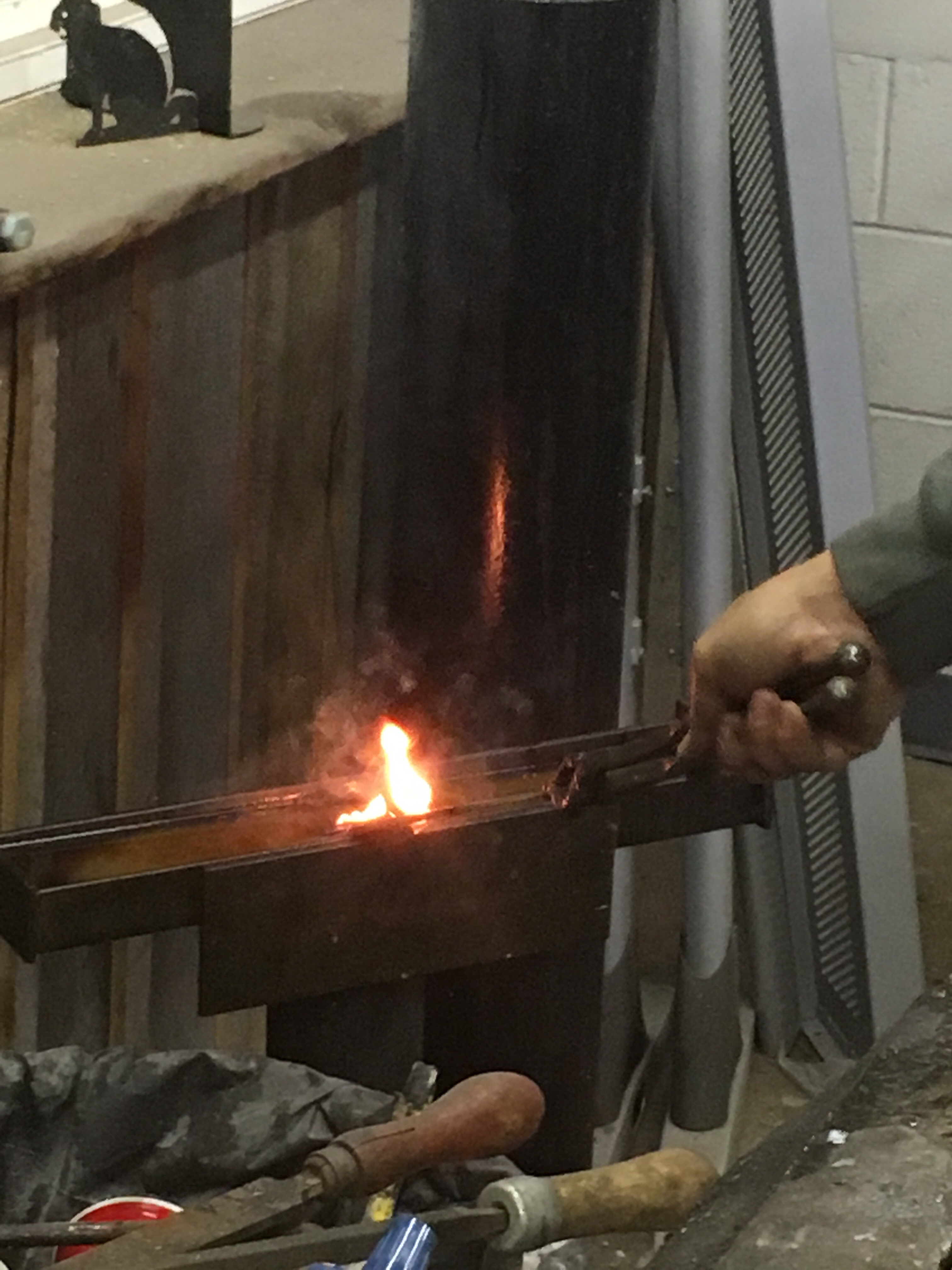
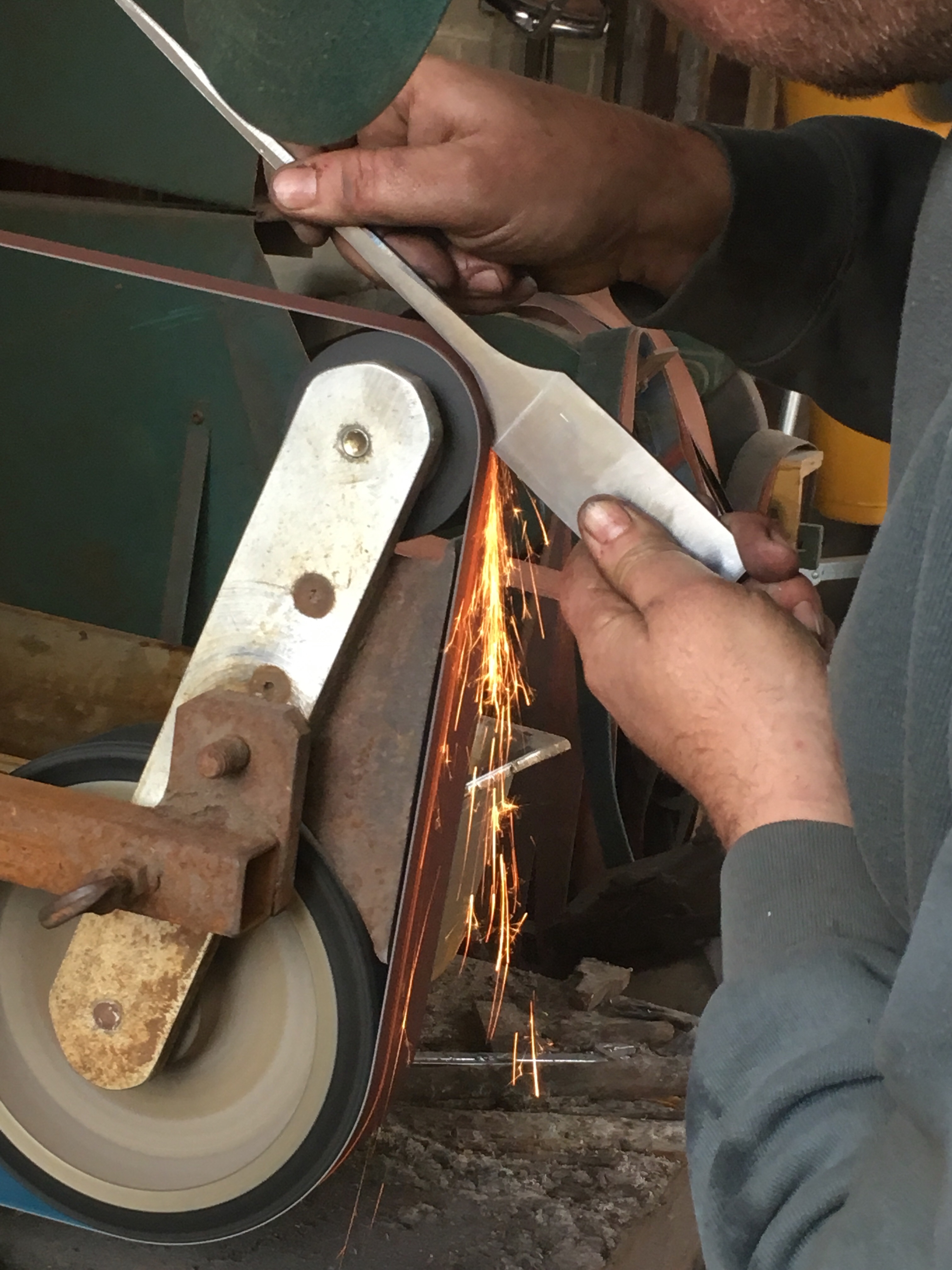
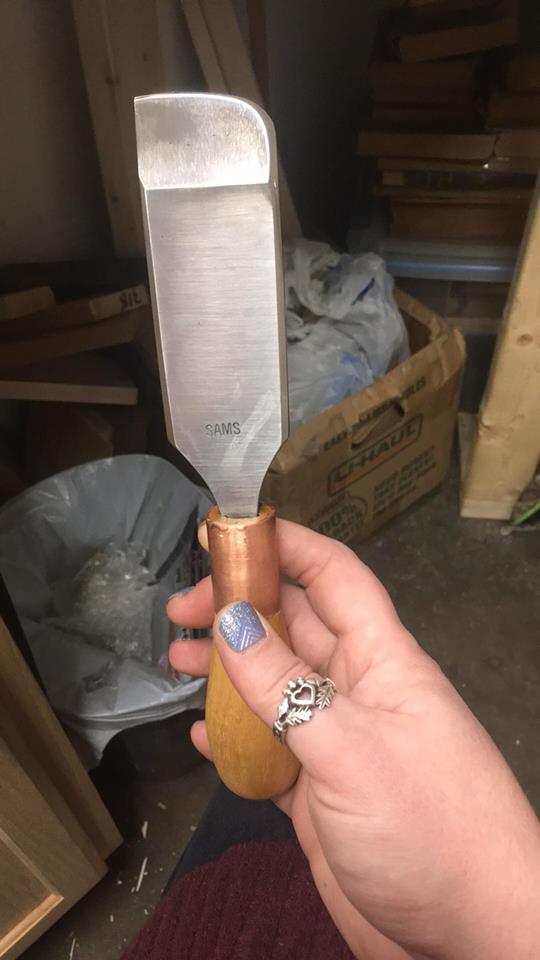
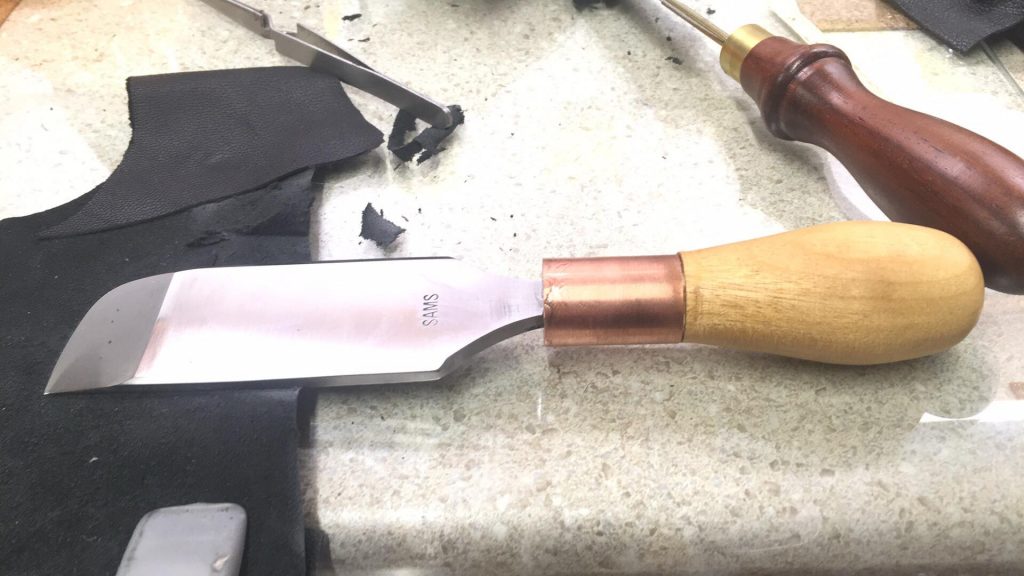
I’d like to thank Carson Sams for inviting us out to his forge and for taking the time to make our custom skiving knife. If you’re ever in need of a particular tool and just can’t find the right one, Carson is excellent at working with you to make and alter it as needed!
(1)
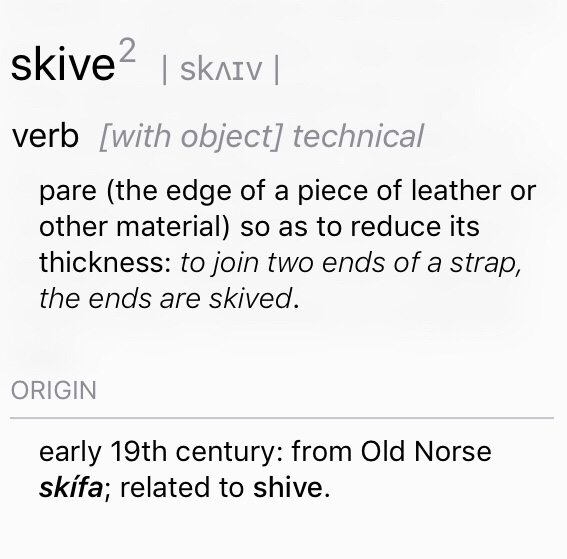
(2)
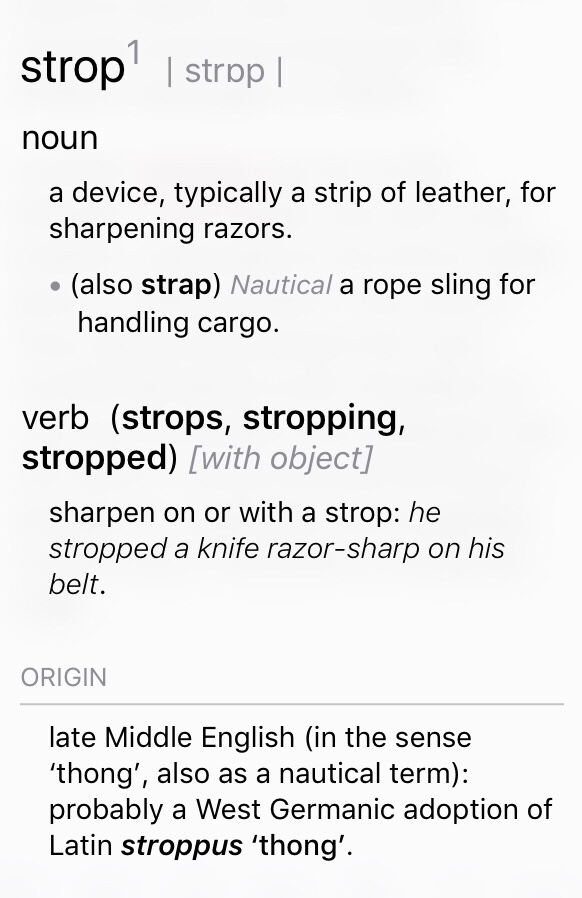